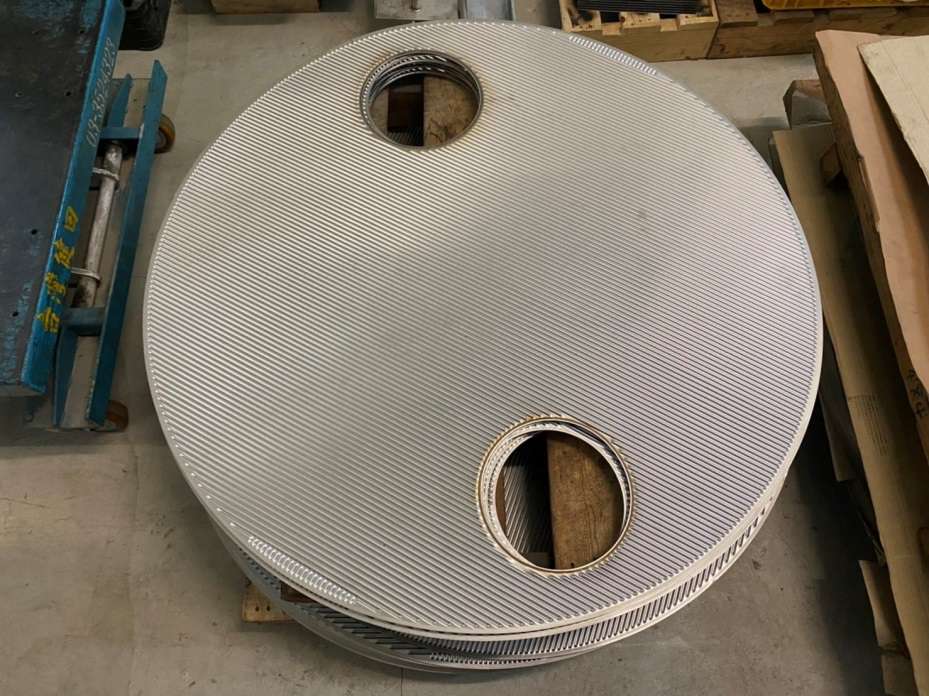
Taiwan SRP Shell & Plate Heat Exchangers - Introduction
In the past, Plate & Gasket type and Shell & Tube type were the majority in the heat exchanger industry. The Plate & Gasket type features high heat transfer efficiency, a small footprint, easy operation, easy hoisting, and easy maintenance; however, the internal gasket is prone to corrosion as time goes by and does not withstand high-temperatures; therefore, leakage incidents are prone to occur.
For the sake of heat transfer effect, plates are usually designed thin; even with thickened plates, they are generally unable to withstand high-pressure environments exceeding 40 Bar.
Although the relatively stable Shell & Tube type may be used in high-temperature and high-pressure work conditions, their footprint is large; they are also difficult to hoist, install, maintain and clean; the weight is high and the heat transfer efficiency is low; they are prone to clog in conditions of specific liquids; plus their price is high and delivery time is long.
Taiwan SRP Inc. has introduced Shell & Plate Heat Exchangers with the combination of merits of the above two types. This new type Heat Exchange features high heat transfer efficiency and high-temperature/pressure resistance, has no internal gasket, and operates steadily; easy to maintain, it provides the opportunity for the customers to opt for new generation heat exchangers.
Applicable to zoned heat supply/refrigeration system, heat ventilation/air-con, power generation/energy storage, bio-fuel and renewable resources, petrochemical industry, oil refinery, natural gas & LNG, waste heat recovery, general steam heating, etc.
Features of SRP Shell and Plate Heat Exchangers
- Site survey by professionals and drawing by a dedicated design team, SRP provides one-stop services from the confirmation of details to delivery of the product.
- Small footprint of product, compact structure design, easy installation, and easy on-site piping.
- Compared to Shell & Plate Heat Exchangers, smaller heat exchanging area and higher heat exchange efficiency.
- No gasket required, eliminating limitations of harsh work conditions that plate type heat exchangers in the past are not suitable for above 200°C or highly corrosive environments.
- High temperature and high pressure, from vacuum to 100 Bar or higher.
- Even fluid distribution.
- The product can be detached for cleaning.
- Laser welded plate core components provide exact and firm plate structures with multiple dimensional options.
- Suitable for evaporator, condenser, radiator and heater applications.
- Option of corrosion resistant plate materials based on work conditions; SRP provides SS304/ SS316L/ S310 / SS904/ SMO254/ Hastelloy C276, Ti, etc.
- The product features a long service lifespan and high flexibility. Serial or parallel design possible for meeting different requirements.
- Versatile selection for suitable port diameter (DN25~DN600)
- Applicable to highly viscose and highly corrosive fluids (e.g. sulfuric acid, etc.)
- Made in Taiwan Quality; short delivery time
- Strict QC, experienced after-sales service force, short maintenance time.
Since its establishment in 1992, Taiwan SRP Inc. has been deeply devoted to servicing the Taiwan marketplace with heat exchangers.
With integrated operation procedures, we offer comprehensive, professional and prompt services, including order reception, interview, delivery, as well as subsequent maintenance and repair.
Taiwan SRP Inc. holds certifications including USA ASME U Stamp, EU Pressure Equipment Directive (PED), American Bureau of Shipping (ABS), Det Norske Veritas/Germanischer Lloyd (DNV/GL), Bureau Veritas (BV), Lloyds Register (LG), China Classification Society (CCS) & China Corporation Register of Shipping (CR) of Taiwan, Lloyds ISO 9001-2015, and EU Welding Certification EN3834-3.
Taiwan Type-I and Pressure Vessel Codes, multiple international specifications are used to comply with review requirements and ensure customer safety when using the device.
Customer Benefits through the use of SRP Shell and Plate Heat Exchangers
- Small device footprint; only 30% compared to traditional shell & tube heat exchangers, saving space for other uses.
- Excellent heat exchange efficiency; one unit replaces multiple traditional ones for thorough heat recovery.
- Lightweight; easy to hoist and install.
- Easy maintenance; Using no gaskets saves costs for the consumables and scheduled maintenance.
- Strong resistance against corrosion; less prone to damage; high availability.
- Competitive costs in production and maintenance.
- Swift maintenance force and after sales service.
Heat exchangers are frequently seen facilities in industries; the most popular models are plate type and shell & plate type. Plate type ones are known for excellent heat transfer efficiency, but using the consumable gasket as fluid segmentation makes them limited by certain work environments having extremely high temperatures or pressures, such as for the storage and transportation of liquefied natural gas (LNG).
Also, gaskets have a limited service lifespan and require periodical maintenance for replacing consumables, where the heat exchanger has to be opened up. The user unit also needs to set up a budget and schedule for subsequent maintenance.
The Shell & Tube type contains no gaskets and is relatively stable, but it is voluminous and requires a large floor area; hoisting and maintenance are uneasy. If used for particular work conditions with special materials, the installation cost is very high; the initial investment will be costly.
The invention of Shell & Plate Heat Exchanger takes and improves advantages of these two; the new type is capable of withstanding high pressure and requires no gaskets while offering high heat transfer efficiency. Plus, with easy maintenance and high equipment availability, it also benefits for a small floor area requirement and less environmental limitations. Having affordable operation costs and a combination of advantages of all the other types, the Shell & Plate Heat Exchanger offers brand new solutions to customers with high-end work conditions.
SPR Shell & Plate Heat Exchangers – Application Fields
- oil and gas industry
- petrochemical industry
- Chemical Industry
- Energy Industry
- Semiconductor industry
- Food industry
- Pharmaceutical industry
- steel mill
- Textile Industry
- Marine
- HVAC
- Hotel, Schools, life water.
(1) Power plant steam turbine radiator, condensate radiator, water supply pre-heater, etc.
(2) Zoned heating, incinerator residual heat recovery for power generation, etc.
(3) Oil cooler of the food industry
(4) Waste heat recovery and slurry warm-up processor of incinerators, sewer systems, etc.
(5) General heater, radiator, condenser and evaporator of the chemical industry.
(6) Petro cooler, circulating evaporator in the petrochemical industry
(7) LNG Desulfurization and LNG storage of LNG industry.
(8) High-pressure refrigeration of ammonia and CO2.
(9) Residual Heat Process of Waste Heat Recovery and ORC systems
SPR Shell & Plate Heat Exchangers – Customer success stories and case studies
Shell & Plate Heat Exchanger used in radiators of Chemical Factories, Taiwan
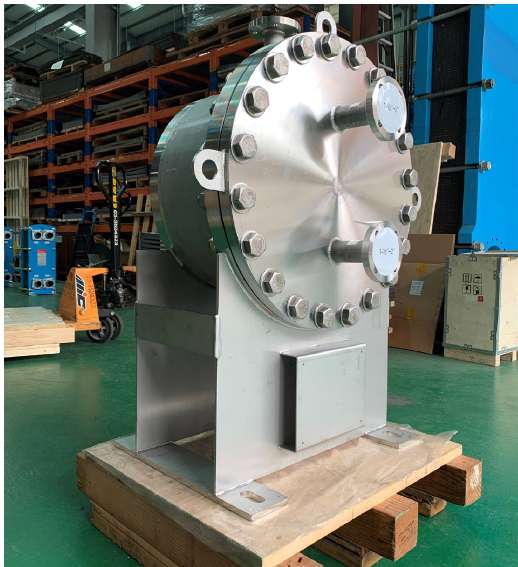
Issues
The Dimethylformamide Process of a customer factory requires cooling, but the process is toxic and unstable.
If a plate type heat exchanger is used, gaskets will age and cause leakage of hazardous liquid into the atmosphere; and the site is limited in space and hoisting is difficult. If Shell & Tube type is opted, the body is too big, also hard to clean.
Application Solution
Customer adopts SRP Shell & Plate Heat Exchanger. The primary side is Dimethylformamide in the liquid phase; the secondary side is water.
In case the liquid leaks, the external side shell design provides protection, preventing hazardous liquid from getting into the atmosphere and causing an incident.
Material: SS304 stainless steel
Total amount of Heat Exchange: 28.16KW
Primary side temperature 20℃-15℃, secondary side temperature 9℃-11.5℃.
- Compared with traditional heat exchangers, light weighted and compact design for space saving and easy installation.
- Affordable price
- Compared with other types of heat exchangers, easy to clean and maintain.
- No gasket used; saves consumable costs.
- Resists high temperature and high pressure. Facility operation not affected.
- Multiple folds heat transfer efficiency than that of traditional heat exchangers.