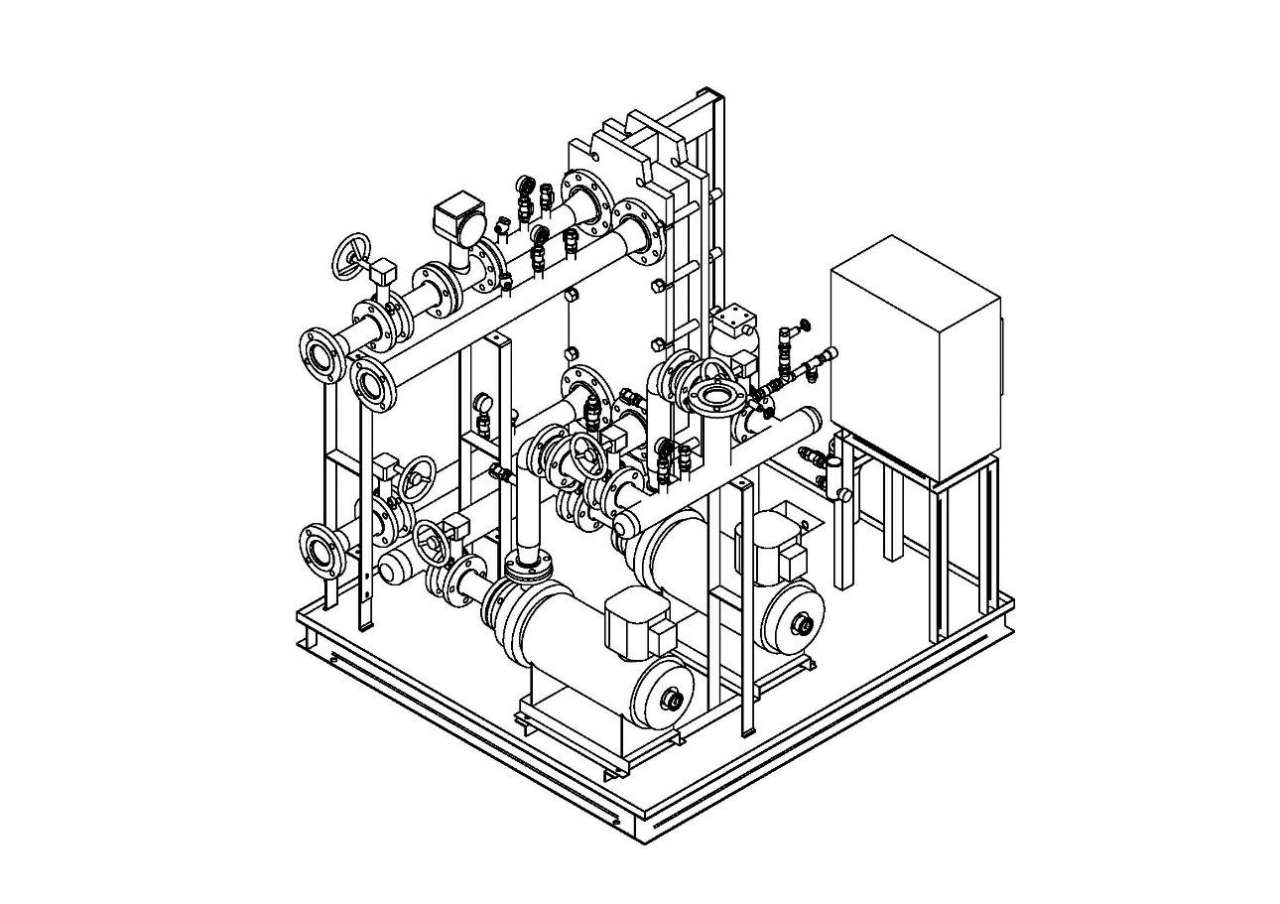
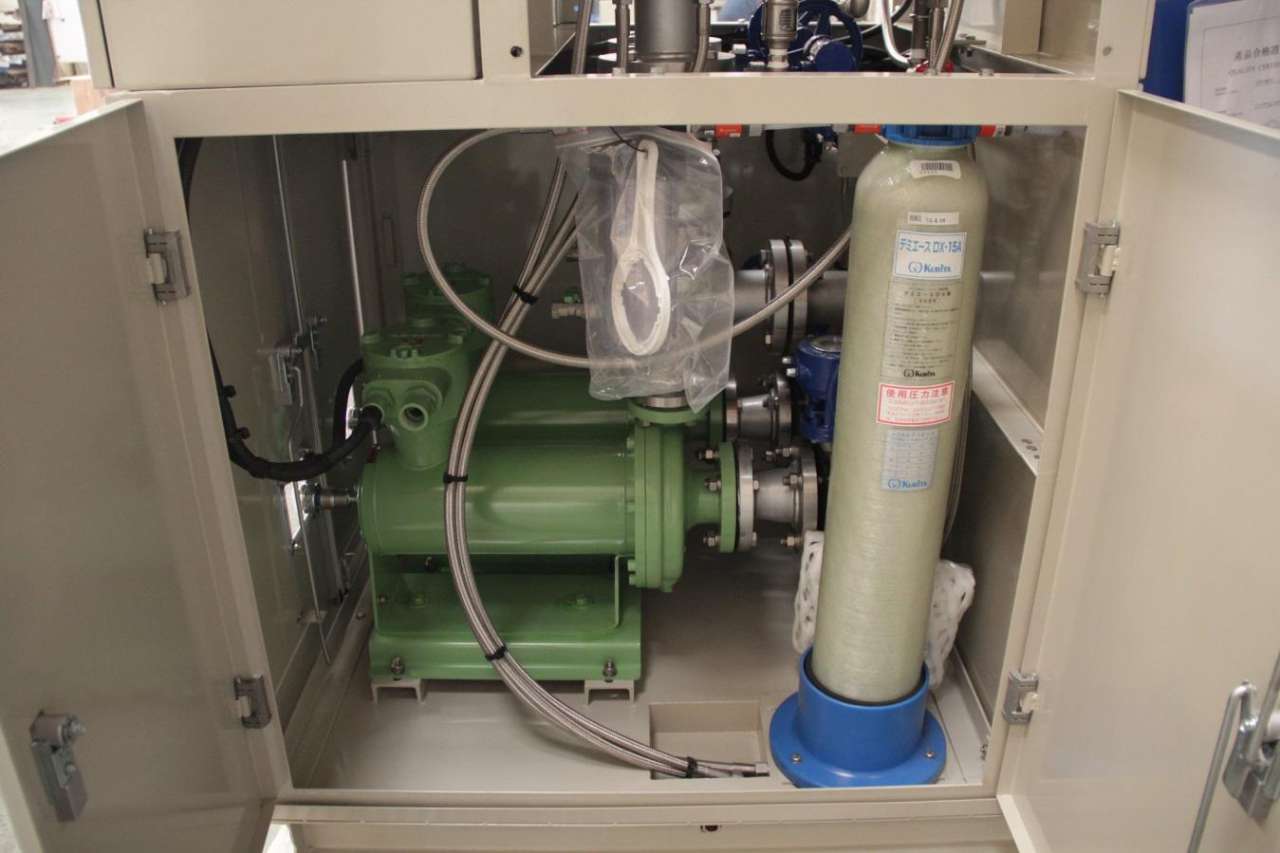
Taiwan SPR Heat Exchanger - Sub-Station Unit - Introduction
Production line standardization and systemization have gradually become the mainstream of factory engineering for accommodating systemization and plant integration in the era of big data to facilitate control of production line progress by Plant Affairs.
This integrated plant is mainly for saving customers’ procurement costs. In the past, when purchasing heat exchangers and accessories, the customer needed to carry out design and coordination with the external contractor regarding piping installation, instrumentation, and even PLC protocol calibration. Those tasks cost significant efforts and resources and the purchase price was very high. It also subjected to inconsistencies between the equipment and actual site conditions and led to disputes over supplier responsibilities.
Heat Exchanging Sub-Station Unit features sophisticated settings and a small footprint. The excellent hardware design results from scientific calculation and optimization. Its Programmable Logic Control (PLC) System is easy to operate, power saving, and environmentally friendly.
It saves the time that customers would otherwise needed to purchase and assemble on their own. It provides a comprehensive and integrated heat exchanging system for customers having different needs.
Applicable to versatile fields including zoned heat supply/refrigeration systems, livelihood hot water systems, heat recycling, seawater desalination, petrochemical engineering, food and wine industry, beverage, electronic manufacturing, pharmaceutical, electricity, metallurgy, and other heat exchange systems.
Features of Taiwan SPR Heat Exchanger - Sub-Station Unit
- SRP provides one-stop services from site survey by professionals, design team drawings, details acknowledgments, and delivery.
- During the manufacturing process, timely liaison and correction will be made with the customer regarding upstream and downstream production parts; the production is transparent and highly flexible.
- Advanced smart touch screen display, PLC design, remote monitoring and simplifies operation allow for centralized management of multiple packages.
- The system is capable of automatic water make-up, automatic pressure release, scale prevention, and stain cleaning.
- Suitable for trades using special liquids, such as refrigeration, food processing, pharmaceutical, chemical, heat recycling boilers, etc.
- Easy to install and operate. Just connect the package with the external piping and perform simple tests, and the system is ready for operation.
- Lightweight product with a small footprint.
- Remote monitoring achievable via mobile phone communication.
- Integral design for turn-key implementation of pipeline installation and accessories purchase/allocation.
- High efficiency heat exchanger; uneasy to accumulate dirt or get clogged.
- Different materials can be selected for the main body of the heat exchanger based on customer needs.
- Long service lifespan. Product has reserved space for expansion/curtailment of plates base on actual needs.
- Strict quality control of products and a well-experienced after-sales service team allow for shortened maintenance time.
Since its establishment in 1992, Taiwan SRP Inc. has been deeply devoted to servicing Taiwan and overseas markets with plate heat exchangers.
With integrated operation procedures, we offer comprehensive, professional and prompt services, including order reception, interview, delivery, as well as subsequent maintenance and repair.
Taiwan SRP Inc. holds certifications including USA ASME U Stamp, EU Pressure Equipment Directive (PED), American Bureau of Shipping (ABS), Det Norske Veritas (DNV), China Classification Society (CCS) & China Corporation Register of Shipping (CR) of Taiwan, Lloyds ISO 9001-2015, and EU Welding Certification EN3834-3. Taiwan Type-I Pressure Vessel Codes and multiple international specifications are used for complying review requirements and ensuring customer safety when using the device.
In recent years, for preventing industrial incidents, the government and labor inspection units tightened inspection of pressure vessel specifications and on-site installations, with relevant statutes and penalty regulations proclaimed more properly.
Taiwan SRP Inc. is one of a few heat exchanger manufacturers in Taiwan qualified for applying certificates of high-pressure gases and Type-I high-pressure vessels.
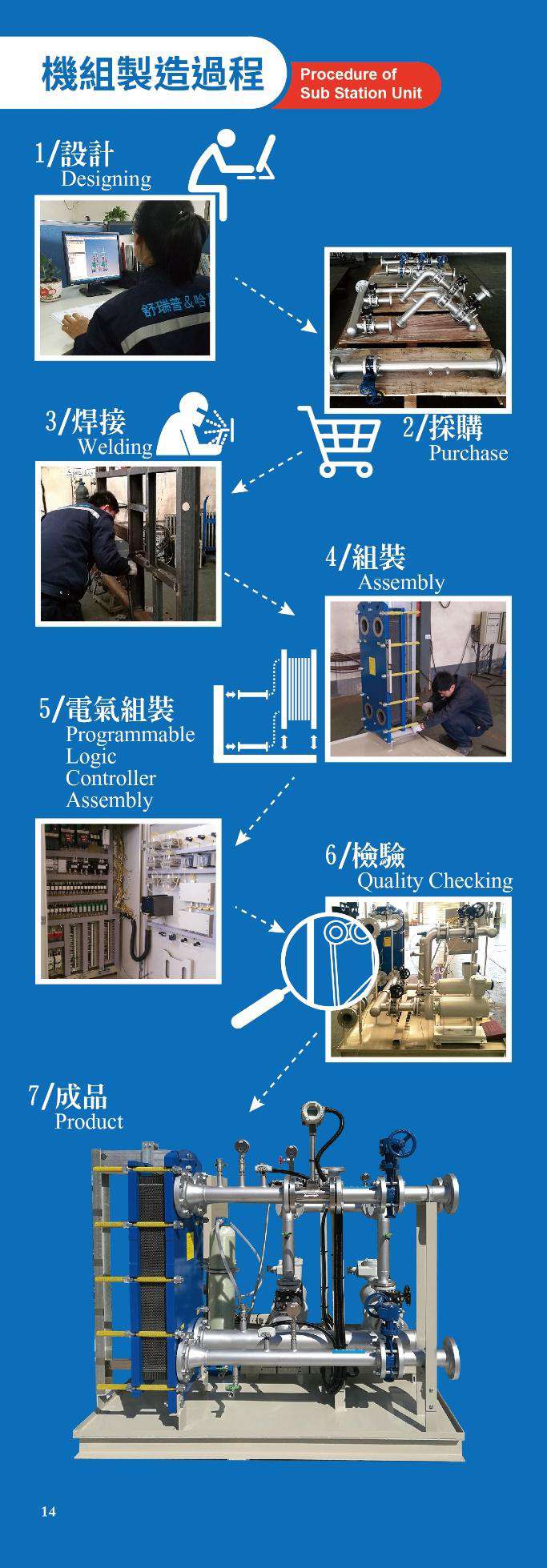
Customer Benefits through the use of SPR Heat Exchanger - Sub-Station Unit
- Competitive price. Effort and time saving for the customer.
- In the past, Plant Affairs, Design and Purchase departments needed to tackle tedious workloads when dealing with external suppliers regarding extra construction costs. Via Heat Exchange - Sub-Station Unit, SRP will take care of all the tasks and save money for the customer.
- Easy to install. Resolves spatial difficulties for the customer.
- Steady water temperature and pressure in the Sub-Station Unit.
- Customer remote control made possible for easy operation.
- Long service lifespan; brief time requirement for annual maintenance.
- Strong resistance against corrosion; less prone to clogged plant. High availability of production line ensures a safe and trouble-free manufacturing process.
- Local (Taiwan) maintenance force and swift after-sales service by dedicated professionals.
In the past, most difficulties for establishing new production line procedures are that Plant Affairs must communicate with respective suppliers and control the actual use of the on-site space; whether for establishing new processes or renewing existing ones, Plant Affairs has to carry out all the tasks for the others. From integral planning to all the tedious tasks regarding valves, pumps, instruments, piping, and others, even linking control terminals of other processes; the proceeding of system integration takes so many days; not to mention to contact different suppliers; even the on-site construction works become extra exertions to the cost.
Via professional planning and experienced practice, the installation of the SRP Heat Exchanger - Sub-Station Unit consists of preliminary site verification, design unit evaluation, combined installation with heat exchangers, and finally, control management of PLC.
Based on customer requirements, the turnkey electromechanical integration significantly saves time costs of Plant Affairs and respective suppliers. Also, the price of accessories lowered by massive procurement provides Plant Affairs with solutions that are time-saving and convenient.
Applications of SRP Heat Exchanger - Sub-Station Unit
- Chemical Industry
- Food industries
- Semiconductor
- Paper and Pulp
- Pharmace utical industry
- HVAC and Refrigeration
- Steel Mill
- Water and Waste Treatment
(1) Chills cooling water of industrial processes.
(2) Hot and cold livelihood water for Restaurant, Hot Spring, School, HVAC, and Swim Pool.
(3) Food industry vacuum sterilization
(4) High-temperature sterilization boiler system of the pharmaceutical industry.
(5) Marine engine radiator, seawater desalination.
(6) Process water recycling of semiconductor industry
(7) Heat storage and heat recycling for respective industrial processes
SRP Heat Exchanger - Sub-Station Unit – Customer success stories and case studies
Heat Exchanging Package used for cooling rectifier of copper foil production line, Taiwan
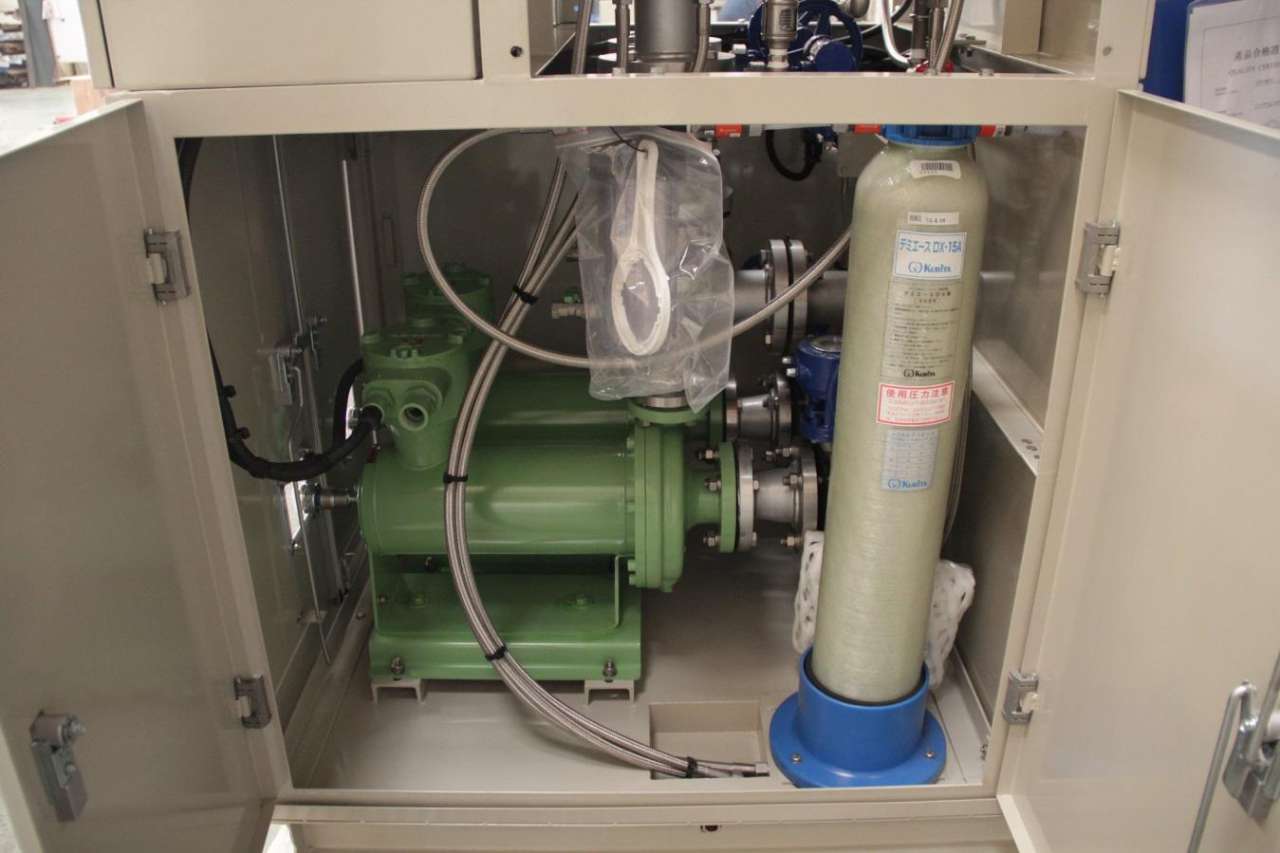
Issues
High voltage rectifier of the copper foil production line requires cooling water for maintaining at a constant temperature, preventing the rectifier from being overheated.
Application Solutions
High voltage rectifier of customer’s copper foil production line requires cooling water for lowering the temperature, and the equipment itself requires a high level of stability. Pure water in the primary side is used as a coolant for the rectifier; a cooling water tower supplies the secondary side as an external source of the coolant.
Water sources of both sides go through a heat exchange process via Heat Exchanging Package, with PLC performing fully automated control at the same time.
In addition to Plate Heat Exchanger, the package is also provided with an ion exchange water treatment facility and conductivity meter for monitoring the quality of cooling water.
Material: 316L full stainless steel. Total heat exchange capacity 130KW.
Water treatment capacity 23328 Kg/H. Port diameter DN100.
Working Temperature: Primary side 46.3℃-40.5.℃; secondary side 32℃-36℃.
- Time and cost-saving; quick integration
- Low footprint of package; affordable cost
- Easy to install and operate
- Allows remote monitoring; real-time feedback of anomaly.
- Highly effective power saving; low operation costs
- Heat Exchanging Package satisfies heat exchange requirements of versatile media in different environments and working conditions.